AS1 Asphalt Additional Modules
Optional modules deliver even more value
as1 PIP – Plant Information Point

The as1 PIP module provides access to key plant data at any time – and from anywhere.
Information such as today’s production quantities, the latest production details, the status of the plant and updates on key components such as the burner and mixer are uploaded to the Ammann cloud.
The data can be accessed from any location, using a browser on the desktop, tablet or smart phone. Even batch protocols are available as a PDF for download.
Highlights
Mobile data solution
Plant KPIs
Latest production information
7-day production trends
Operating data
Plant status info (e.g., bitumen tank temperature)
Daily trend data
Batch protocol PDFs
Upgradeable to Q Plant solution;
as1 Loadout

The right load is important
The as1 Loadout module is the logical complement of the as1 production control system. The enlarged view of the loadout silos offers additional information such as time stamps of the last filling and take out, silo content and last loaded quantity. The view comes either on the main screen, a second screen or optionally on a separate workstation for the truck loading operator.
Highlights:
Large display of the loadout silos
Efficient and safe loading
Increased safety thanks to integrated tare verification and overload protection of the vehicles
Automatic level calculation of the loadout silos
as1 Traffic Control (TC)

Who is next
The loading order is relayed to drivers and operators via a large display.
Highlights:
Less communication via radio
Automatic display of silo and truck information
No traffic jam before weigh bridge
Optimised process flow
as1 Weighing System

Automatic delivery note generation
The as1 truck weighing system can be used to create weighing orders, weigh vehicles, and create delivery notes. The delivery note data can be transferred electronically into the invoicing system by means of data transfer, which reduces the amount of administrative work considerably. The truck weighing system can be operated as a stand – alone system or it can be combined with the as1 loadout system and integrated into an as1 process control system.
Highlights:
Integrated master data handling
Direct delivery note creation
Integrated delivery statistics
Fully integrated with as1 control system
Reduction of administration costs thanks to electronic data transfer into the invoicing system
Overload protection in combination with as1 loadout system
as1 Driver Terminal

Easy registration
The system can be supplemented with a card-based identification process to aid the operator.
Highlights:
Optimised process flow
Less communication via radio
Available with RFID cards and PIN codes
Self registration when arriving at plant
Available with ticket printer in combination with as1 Weighing System
as1 Dynamic Recycling Addition (RAD)

Various RAP ratios in a single recipe
Use of reclaimed asphalt protects natural resources and also offers economical advantages. The optional as1 module “dynamic RAP addition“ makes it easy to modify the RAP ratio in accordance with requirements, even during production.
Two compensation options
Quantitative compensation
The correction of virgin material is carried out in relation to the quantity and composition of the RAP material.
Qualitative compensation
The correction of virgin material is carried out in relation to the quantity and composition of the RAP material in accordance of Ring and Ball specifications (based on the formulae detailed in EN13108).
Highlights:
The integrated wizard guides operator through the recipe input process
One recipe is sufficient for numerous RAP ratios
Changing the RAP ratio by using the slide controls during production
as1 Ecoview

Energy efficiency made visible
EcoView promotes energy optimisation and helps to uncover and eliminate waste.
The module provides straightforward information about energy consumption and CO₂ emission values. It can compare fresh and historical data to identify trends.
Highlights:
Intuitive operator display showing how efficient the plant runs
Displays key values and enables comparison to reference values and previous periods
Determines the emitted CO₂ values
Determines the resulting energy costs
as1 Peak Load (PLM)

Peak load management
Utilities often charge based on the measured peak. This module helps keep that peak as low as possible.
The system continuously monitors peak performance against critical values and predicts peak fee times. The goal is to reduce the peak load at the most expensive time of the day. This can be accomplished by managing certain processes, such as heating, based on the forecast of the most expensive times to consume energy.
The module fits seamlessly in the as1 eco modules and is available for the gas and electricity.
Highlights:
Preventing short term and expensive electrical peak loads
Forecast function
Automatic switch off for electrical consumers
as1 Excel Addin

Indispensable for in-depth evaluations of as1 data in Excel
Ammann offers an AddIn for Excel for comprehensive data evaluation, as an extension of the broad menue of as1 standard reports. This ingenious tool makes your Excel as1-capable. This enables the desired data to be imported into Excel where it can then be processed just as you wish.
Highlights:
The requisite data can be selected from the comprehensive as1 data pool, imported into
Excel and then evaluated
Newly generated data can be seamlessly integrated at any time with a click of the mouse
An effective tool for your individual evaluations in one trusted tool
as1 Integrated Maintenance Management (IMM)

Maintenance due?
The as1 IMM Module supports the staff with the planning of the required maintenance tasks of the mixing plant. The module allows various maintenance tasks to be created and structured. Supported are maintenance tasks with fixed time schedules as well as event based tasks which are automatically planned based on the operating hours or the quantities processed on the plant. Store documents like work instructions or even short video clips to each single maintenance task.
Highlights:
Planning of cyclic maintenance tasks
Planning of event based maintenance tasks
Listing of the due maintenance tasks
Cost registration of the maintenance tasks
Assignment of detailed, multimedia work instructions
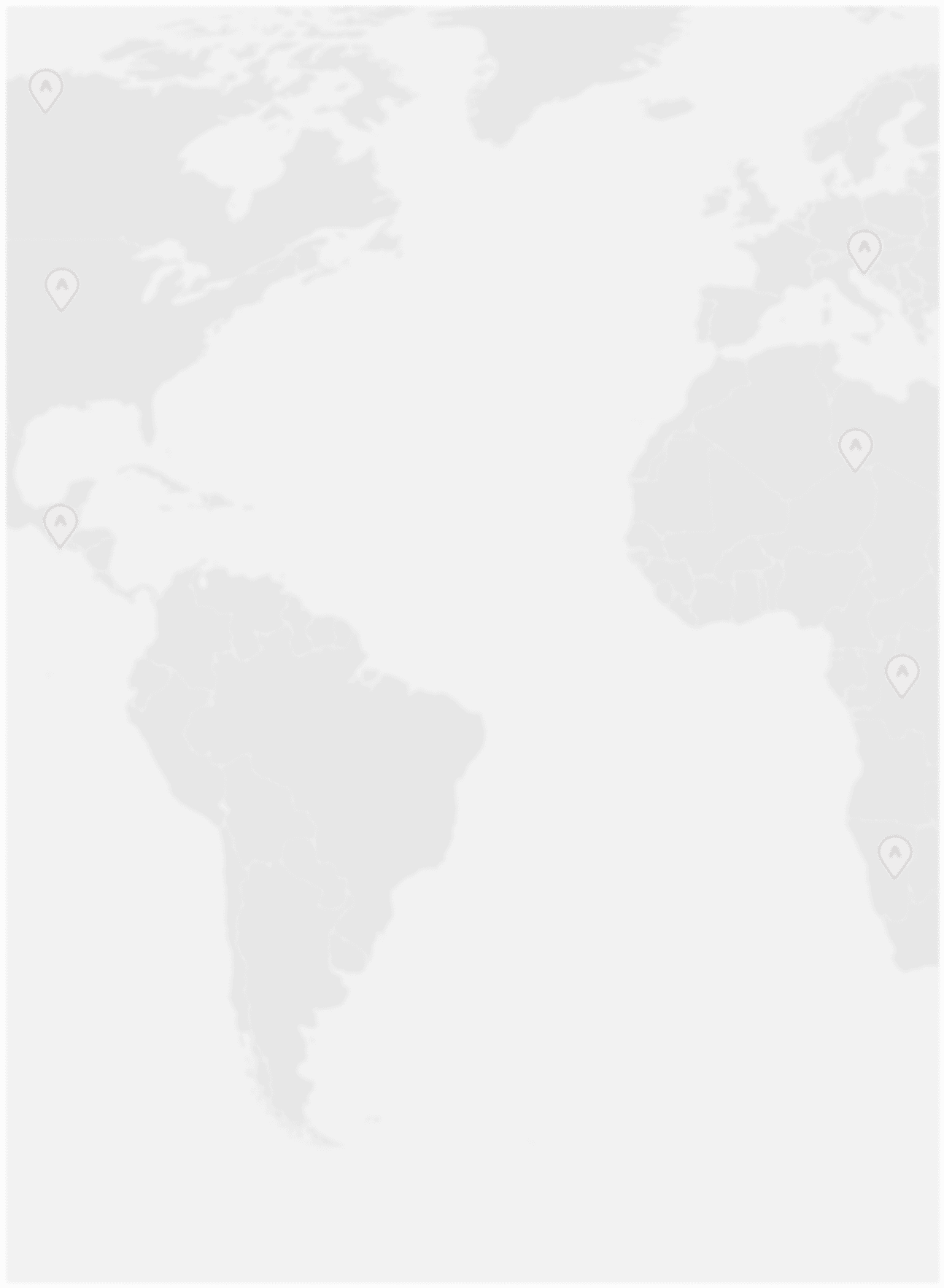
Contact Form
Schedule online meeting
Get in touch with us to meet a sales representative near you
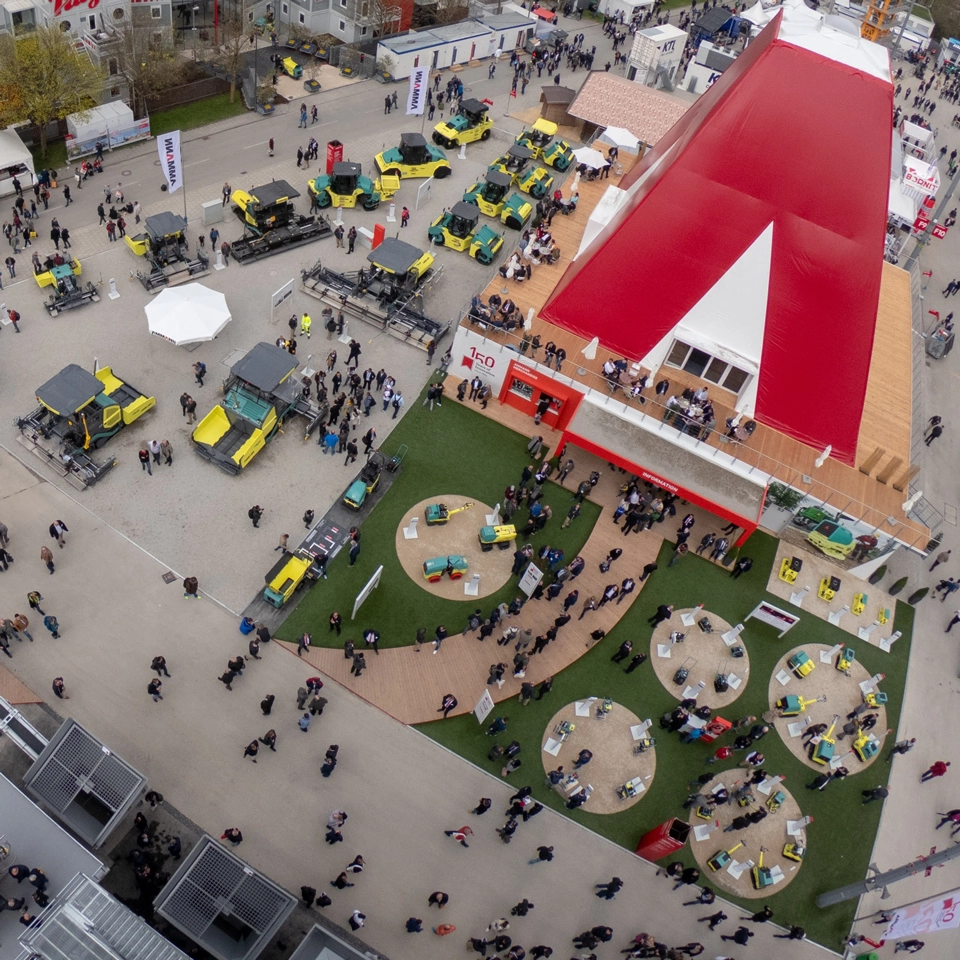